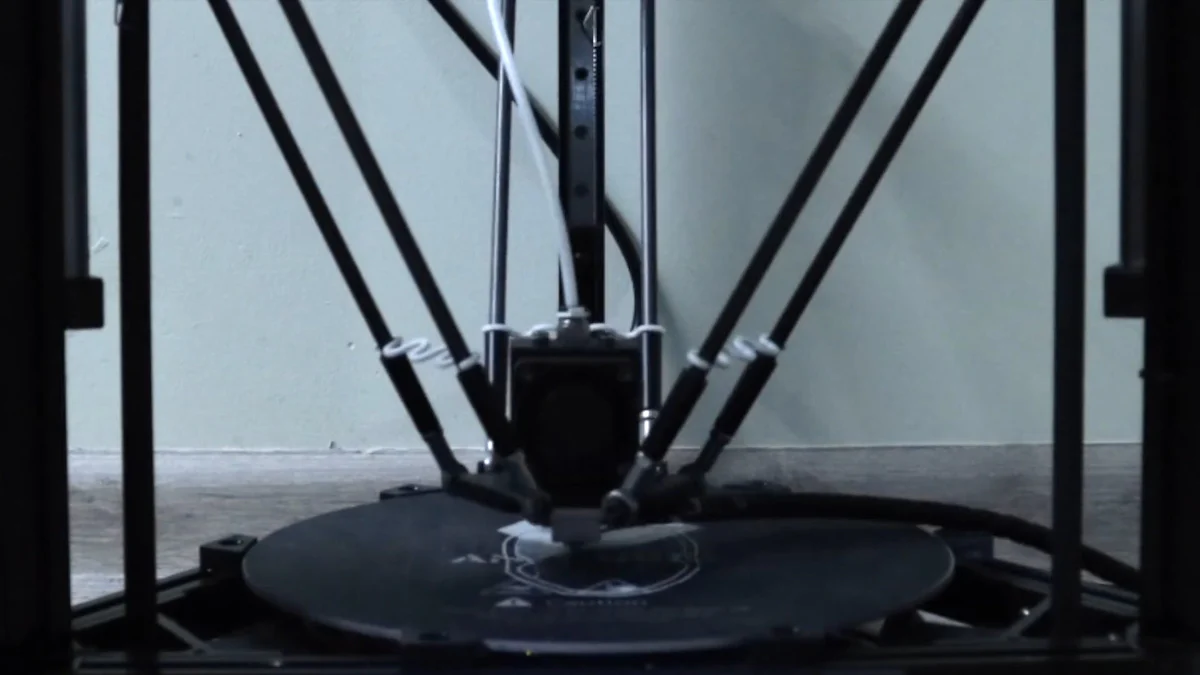
Imagine holding a miniature version of your favorite character or a custom figure that you've designed yourself. With the rise of custom 3D printing figures, this dream is now a reality. The 3D printing market is booming, with a projected growth rate of 22.66% annually. This technology allows you to transform your ideas into tangible models. You can choose from a variety of materials and colors to create something truly unique. Whether you're a hobbyist or a professional, the possibilities are endless. Dive into the world of 3D printing and unleash your creativity.
Key Takeaways
-
Custom 3D printing allows you to transform your ideas into unique, tangible models, whether for personal enjoyment or professional use.
-
Understanding the different types of 3D figures—action figures, miniatures, and figurines—can help you choose the right project for your interests.
-
Personalization is key; customizing your 3D figures adds a meaningful touch, making them perfect gifts or collectibles.
-
Familiarize yourself with CAD software and online design platforms to effectively create and refine your 3D models.
-
Choosing the right materials, such as PLA, ABS, or resin, is crucial for achieving the desired quality and functionality in your prints.
-
Follow a step-by-step process from sketching your design to post-processing your print to ensure a successful outcome.
-
Engage with the supportive 3D printing community for resources, advice, and inspiration as you explore your creative potential.
Understanding Custom 3D Printing Figures
Custom 3D printing figures have revolutionized the way you can create and enjoy personalized models. Whether you're a fan of action figures or love collecting miniatures, this technology offers endless possibilities. Let's dive into the different types of 3D figures and their popular uses.
Types of 3D Figures
Action Figures
Action figures are dynamic and often depict characters from movies, comics, or video games. You can design your own hero or villain, complete with intricate details and vibrant colors. These figures are perfect for collectors who want something unique on their shelves.
Miniatures
Miniatures are small-scale models that capture fine details. They're popular in tabletop games and dioramas. You can create custom miniatures to enhance your gaming experience or to display as part of a collection. The precision of 3D printing ensures that even the tiniest features stand out.
Figurines
Figurines can represent anything from animals to abstract shapes. They serve as decorative pieces or personalized gifts. With 3D printing, you can bring your imagination to life, crafting figurines that reflect your personality or interests.
Popular Uses and Applications
Collectibles
Custom 3D printing figures make excellent collectibles. You can design figures that are one-of-a-kind, adding a personal touch to your collection. Whether it's a beloved character or a unique creation, these figures hold sentimental value.
Prototyping
In product design, 3D modeling software helps you create prototypes. You can test the aesthetics and ergonomics of items before production. This process allows for quick iterations and adjustments, saving time and resources.
Educational Models
Educational models benefit greatly from custom 3D printing. You can create detailed replicas of historical artifacts, anatomical models, or scientific structures. These models enhance learning by providing a tangible representation of complex concepts.
Custom 3D printing figures offer a world of creativity and functionality. Whether you're designing action figures, miniatures, or figurines, the possibilities are endless. Embrace this technology to create something truly special.
The Customization Process
Creating custom 3D printing figures is an exciting journey that lets you bring your unique ideas to life. This process not only allows you to personalize your creations but also offers a platform for creative expression. Let's explore the benefits of customization and the tools you'll need to get started.
Benefits of Customization
Personalization
When you design custom 3D printing figures, you have the power to make something truly yours. Personalization means you can tailor every aspect of your figure, from its size and shape to its color and texture. Imagine gifting a friend a miniature version of their favorite pet or creating a model of a beloved character with your own twist. Personalization adds a special touch that makes each figure unique and meaningful.
Creative Expression
Customizing 3D figures is a fantastic way to express your creativity. You can experiment with different designs, try out new ideas, and push the boundaries of what's possible. Whether you're an artist looking to showcase your work or a hobbyist eager to explore new concepts, 3D printing offers a canvas for your imagination. The ability to create something from scratch and see it come to life is incredibly rewarding.
Tools and Software for Custom Design
To start designing your custom 3D printing figures, you'll need the right tools and software. These resources will help you transform your ideas into detailed models ready for printing.
CAD Software
Computer-Aided Design (CAD) software is essential for creating precise and intricate designs. Programs like Tinkercad, Fusion 360, and Blender offer a range of features that cater to both beginners and experienced designers. With CAD software, you can draft, modify, and refine your models with ease. It provides the flexibility to adjust dimensions, add details, and ensure your design is print-ready.
Online Design Platforms
If you're new to 3D design or prefer a more user-friendly approach, online design platforms are a great option. Websites like Thingiverse and Shapeways offer tools that simplify the design process. These platforms often include templates and community-shared designs that you can customize to suit your needs. They make it easy to experiment with different styles and collaborate with other creators.
Expert Testimony: An expert in 3D printing technology highlights the integration of this technology with fields like digital medicine and materials science. This multidisciplinary approach allows for the creation of customized prosthetics, enhancing precision and satisfaction in clinical applications.
By leveraging these tools and embracing the customization process, you can create custom 3D printing figures that reflect your vision and creativity. Whether you're crafting a personalized gift or exploring new artistic avenues, the possibilities are endless.
Essential Tips Before Starting
Before you dive into the world of custom 3D printing figures, it's crucial to understand the materials and printer capabilities. These factors significantly impact the quality and success of your projects.
Choosing the Right Materials
Selecting the right material is a key step in 3D printing. Each material offers unique properties that can affect the final outcome of your figure.
PLA
PLA (Polylactic Acid) is a popular choice for beginners. It's biodegradable and made from renewable resources like corn starch. PLA is easy to print with and produces a smooth finish. It works well for decorative items and prototypes. However, it might not be the best choice for objects that need to withstand high temperatures or stress.
ABS
ABS (Acrylonitrile Butadiene Styrene) is known for its strength and durability. It comes in various colors, making it ideal for vibrant and sturdy models. ABS is great for functional parts and toys. However, it requires a heated bed and emits fumes during printing, so ensure proper ventilation.
Resin
Resin is perfect for highly detailed and smooth objects. It captures intricate features with precision, making it suitable for miniatures and figurines. Resin printing involves a different process than filament-based printing, often requiring post-processing like curing. It's ideal for applications where fine details matter most.
Understanding Printer Capabilities
Knowing your printer's capabilities helps you achieve the best results. Different printers offer varying features that can influence your design choices.
Printer Types
There are several types of 3D printers, each with its own strengths. FDM (Fused Deposition Modeling) printers are common and user-friendly, suitable for most hobbyists. SLA (Stereolithography) printers use resin and are excellent for detailed prints. Choose a printer that aligns with your project's needs and your experience level.
Print Resolution
Print resolution determines the level of detail in your model. Higher resolution means finer details but longer print times. Consider the complexity of your design when setting the resolution. For intricate custom 3D printing figures, a higher resolution ensures that every detail stands out.
By understanding these essential tips, you set yourself up for success in creating custom 3D printing figures. Choose the right materials and familiarize yourself with your printer's capabilities to bring your creative visions to life.
Step-by-Step Guide to Creating and Printing
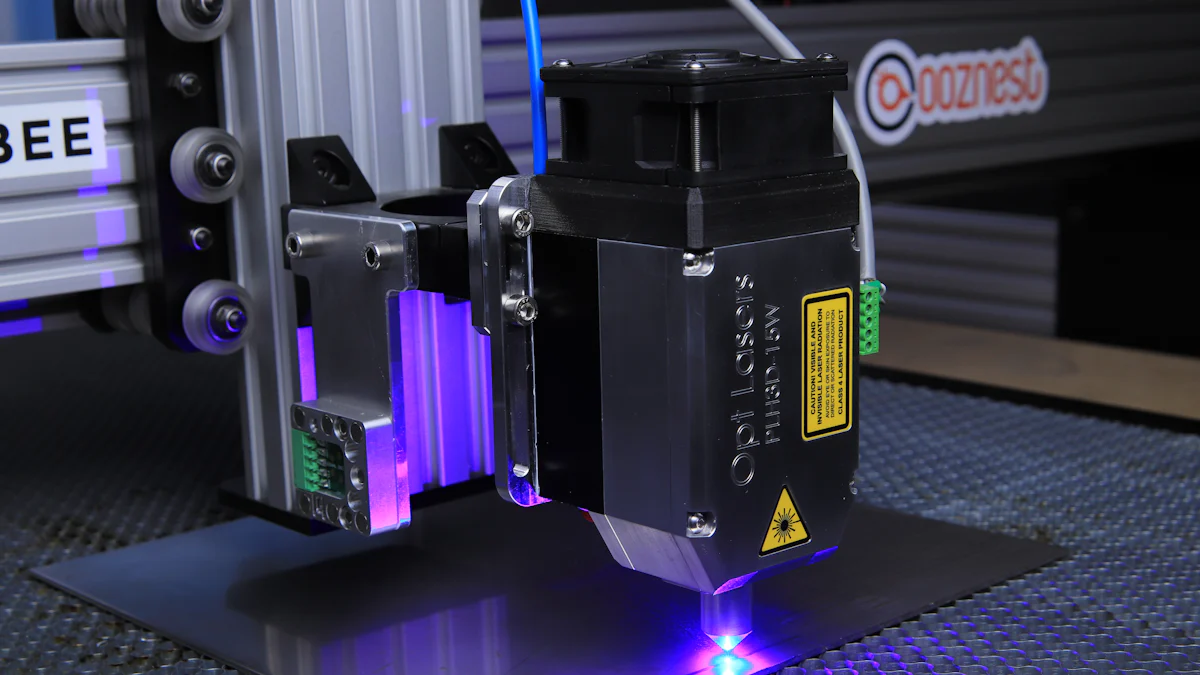
Creating custom 3D printing figures is an exciting journey. Let's break it down into simple steps to help you bring your ideas to life.
Designing Your 3D Model
Sketching and Conceptualizing
Start with a sketch. Grab a pencil and paper, and let your imagination flow. Sketching helps you visualize your idea. Think about the shape, size, and details of your figure. This step is crucial because it lays the foundation for your design.
Using Design Software
Once you have a clear concept, it's time to use design software. Programs like Tinkercad or Fusion 360 are great for beginners. They allow you to create precise models. You can adjust dimensions, add details, and ensure your design is ready for printing. Remember, practice makes perfect. The more you use these tools, the better you'll get.
Preparing the 3D Printer
Setting Up the Printer
Before you start printing, set up your 3D printer. Place it on a stable surface. Ensure all parts are secure. Load the filament or resin, depending on your printer type. Follow the manufacturer's instructions for the best results.
Calibrating the Printer
Calibration is key to a successful print. Adjust the printer's settings to match your design's requirements. Check the bed level and nozzle height. Proper calibration ensures that your custom 3D printing figures come out just right.
Printing and Post-Processing
Printing the Model
Now, it's time to print. Send your design to the printer and watch it come to life. This process can take some time, so be patient. Keep an eye on the print to ensure everything runs smoothly.
Finishing Touches
Once printing is complete, it's time for finishing touches. Remove the model from the printer carefully. If you're using resin, cure it according to the instructions. Sand any rough edges and paint your figure if desired. These final steps add polish and make your figure truly unique.
Madeline Hogan, a specialist in resin 3D printing, emphasizes the importance of post-processing. She notes that "finishing touches can transform a good print into a great one."
By following these steps, you can create stunning custom 3D printing figures. Each stage, from sketching to finishing, plays a vital role in bringing your vision to life. So, grab your tools and start creating!
Troubleshooting Common Issues
When you're diving into the world of 3D printing, encountering a few hiccups is pretty normal. But don't worry! With a bit of know-how, you can tackle these challenges head-on. Let's explore some common issues and how you can fix them.
Print Quality Problems
Layer Shifting
Layer shifting can be a real headache. It happens when the layers of your print don't align properly, resulting in a skewed model. To fix this, check the belts and pulleys on your printer. They should be tight and secure. Loose belts can cause the print head to move unexpectedly, leading to misaligned layers. Also, ensure that the printer is on a stable surface to prevent vibrations during printing.
Warping
Warping occurs when the edges of your print lift from the print bed, distorting the model. To combat this, make sure the print bed is level and clean. You can also use a heated bed to help the first layer adhere better. Applying a thin layer of adhesive, like glue stick or painter's tape, can also improve bed adhesion. If warping persists, try adjusting the print temperature or slowing down the first layer speed.
Software and Hardware Issues
Software Crashes
Software crashes can disrupt your workflow and waste valuable time. To minimize these, keep your design software updated. Updates often fix bugs and improve performance. Save your work frequently to avoid losing progress. If crashes continue, check for compatibility issues with your operating system or consider using alternative software.
Printer Malfunctions
Printer malfunctions can be frustrating, but they're often solvable. Start by checking the printer's connections and cables. Loose or damaged cables can cause communication errors. Regular maintenance, like cleaning the nozzle and lubricating moving parts, can prevent many issues. If the printer still doesn't function as expected, consult the manufacturer's troubleshooting guide or seek professional support.
Pro Tip: Documenting your troubleshooting process can be invaluable. Keep a log of the issues you encounter and the solutions you try. This record can help you identify patterns and find quicker solutions in the future.
By understanding these common issues and their solutions, you can keep your 3D printing projects on track. Remember, practice makes perfect, and each challenge is an opportunity to learn and improve your skills. Happy printing!
Exploring Advanced Techniques
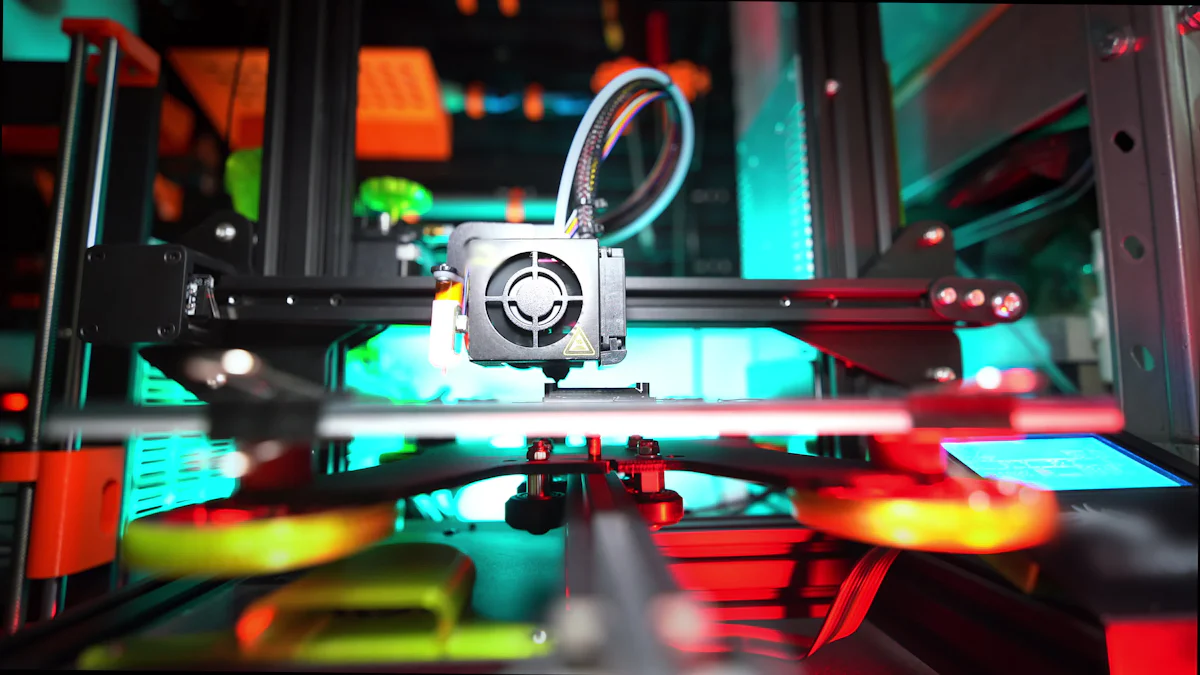
As you delve deeper into the world of 3D printing, you'll discover advanced techniques that can elevate your creations to new heights. These methods allow you to experiment with different materials and add intricate details to your models. Let's explore some of these exciting possibilities.
Multi-Material Printing
Multi-material printing opens up a world of creativity by allowing you to use more than one material in a single print. This technique can enhance the functionality and aesthetics of your models.
Dual Extrusion
Dual extrusion is a popular method for multi-material printing. It involves using two extruders to print with different materials or colors simultaneously. You can create complex models with varying textures or colors without needing to assemble separate parts. Imagine printing a figure with a flexible joint or a colorful pattern directly onto the model. Dual extrusion makes it possible to achieve these effects seamlessly.
Mixing Materials
Mixing materials in 3D printing can lead to innovative designs and applications. By combining materials with different properties, you can create parts that are both strong and lightweight or flexible and durable. For example, you might print a model with a rigid frame and a soft exterior, perfect for creating functional prototypes or unique artistic pieces. This approach allows you to tailor the material properties to suit your specific needs.
Scientific Research Findings: A new 3D printing method enables the creation of multi-material parts with spatially tunable, multi-scale porosity. This advancement allows for greater customization and functionality in printed models.
Adding Color and Texture
Adding color and texture to your 3D prints can bring them to life, making them more visually appealing and realistic. These techniques allow you to personalize your models further.
Painting Techniques
Painting your 3D prints is a fantastic way to add color and detail. You can use acrylic paints, spray paints, or even airbrushes to achieve the desired effect. Start by applying a primer to ensure the paint adheres well to the surface. Then, use thin layers of paint to build up the color gradually. Experiment with different brushes and techniques to create shading, highlights, and intricate patterns. Painting transforms a plain model into a vibrant masterpiece.
Texturing Methods
Texturing adds depth and realism to your 3D prints. You can use various methods to create textures, such as applying textured paint or using a heat gun to warp the surface slightly. Another approach is to design the texture directly into the model using CAD software. This method allows you to incorporate intricate patterns or simulate materials like wood or stone. Texturing enhances the tactile and visual appeal of your models, making them stand out.
By exploring these advanced techniques, you can push the boundaries of what's possible with 3D printing. Whether you're experimenting with multi-material printing or adding color and texture, these methods offer endless opportunities for creativity and innovation. So, grab your tools and start exploring the exciting world of advanced 3D printing techniques!
Creating custom 3D printing figures is an exciting journey. You get to see your ideas come to life. The process is straightforward and rewarding. You can start your own project today. The 3D printing community is supportive and accessible. You'll find plenty of resources and advice. Dive in and explore the endless possibilities. Your creativity is the only limit. So, grab your tools and start designing. The world of custom 3D printing figures awaits you.
FAQ
What is the best material for 3D printing figures?
Choosing the right material depends on your project's needs. PLA is great for beginners due to its ease of use and smooth finish. ABS offers strength and durability, making it ideal for functional parts. For intricate details, resin is your best bet. Each material has unique properties, so consider what suits your design best.
Can I use metal for 3D printing?
Yes, you can use metal in 3D printing. Metal 3D printing involves processes like Direct Metal Laser Sintering (DMLS) or Selective Laser Melting (SLM). These methods allow you to create strong and durable metal parts. However, they require specialized equipment and expertise. If you're considering metal 3D printing, ensure it's the right process for your needs.
How do I start designing my own 3D figures?
Begin with a sketch to visualize your idea. Use design software like Tinkercad or Fusion 360 to create a digital model. These tools help you refine your design and prepare it for printing. Practice and experimentation will improve your skills over time.
What are the common issues in 3D printing, and how can I fix them?
Common issues include layer shifting and warping. To fix layer shifting, check your printer's belts and pulleys. For warping, ensure the print bed is level and clean. Use a heated bed or adhesive to improve adhesion. Regular maintenance and calibration can prevent many problems.
How can I add color to my 3D prints?
You can add color by painting your 3D prints. Use acrylic paints or spray paints for the best results. Start with a primer, then apply thin layers of paint. Experiment with different techniques to achieve the desired effect. Painting adds a personal touch to your models.
What software should I use for 3D modeling?
For beginners, Tinkercad is user-friendly and easy to learn. Fusion 360 offers more advanced features for experienced designers. Blender is another option for creating detailed models. Choose software that matches your skill level and project requirements.
How do I choose the right 3D printer?
Consider your project's needs and your experience level. FDM printers are common and user-friendly, suitable for most hobbyists. SLA printers offer high resolution for detailed prints. Research different models and read reviews to find the best fit for you.
Can I print multi-material models?
Yes, you can print multi-material models using dual extrusion. This technique allows you to use two materials or colors in a single print. It enhances the functionality and aesthetics of your models. Experiment with different combinations to achieve unique effects.
How do I ensure my 3D prints are high quality?
Ensure your printer is properly calibrated and maintained. Choose the right material and print settings for your design. Pay attention to details like print resolution and bed adhesion. Regular practice and experimentation will improve your print quality over time.
Where can I find resources and support for 3D printing?
The 3D printing community is supportive and accessible. Online forums, tutorials, and social media groups offer valuable resources and advice. Websites like Thingiverse and Shapeways provide design inspiration and collaboration opportunities. Dive in and explore the endless possibilities!
See Also
Crafting Unique Figurines: A Personal Design Journey
Building Custom Action Figures Tailored Just for You
Your Ultimate Guide to Personalizing Roblox Characters
Simple Tips for Customizing Your Roblox Figures
Discovering the Legendary Characters of Marvel Figure Factory